Vibration Isolation for Heavy
Payload Systems
Minus K vibration isolation systems can be
designed for very heavy payloads. The following are some typical isolator
dimensions. The 10,000 lb and 25,000 lb isolator dimensions are approximate and
are based on preliminary designs.
XM-1:
10,000 lb capacity: 20"W x 20"D x 22"H
The James Webb Space Telescope is the largest
cryogenic instrument telescope to be developed for space flight. It is a
large-aperture infrared space telescope and the scientific successor to NASA's
Hubble Space Telescope and used a set of six custom heavy capacity Minus K
vibration isolators for ground testing.
The ground testing confirmed
the telescope and science instrument systems will perform properly together in
the cold temperatures of space. Additional test support equipment including
mass spectrometers, infrared cameras and television cameras were also supported
by Minus Ks heavy capacity vibration isolators which allowed engineers to
observe the testing.
Each of the isolators was designed for 10,000 lbs.
and the total payload supported from the top of the Johnson Space Center vacuum
Chamber A was 60,000 lbs.
The isolators allowed NASA to simulate the
telescopes performance in space while preventing all the ground-based
disturbances, such as the pumps and motors, and even traffic driving by from
interfering with the ground testing.
Case study:
NASA James Webb Space Telescope
(JWST).
|
Featured Product: SM-1 Large Capacity, Low Frequency Vibration
Isolators
- Vertical natural frequency of 1/2 Hz or less can be achieved over the
entire load range.
- Horizontal natural frequency is load dependent. 1/2 Hz or less can be
achieved at or near the nominal load.
- See typical transmissibility curve
Performance for the SM-1.
Minus
K's
SM-1 is low frequency vibration isolator for weight
loads from 500 to 4200 lbs. and 1/2 Hz performance vertical and horizontal.
The SM-1 negative-stiffness isolator is the basic building block of the
FP-1 Floor Platform and other heavy multiple
isolator systems. They require no air or electricity.
This isolator has
the same basic features of our all passive, negative-stiffness,
manually-adjustable bench top isolators. It offers our very-low frequency
isolation performance for payloads of many thousands of pounds.
SM-1 isolator can be used alone or with any number
of additional units to achieve higher capacity systems. They can be arranged in
many geometrical configurations to suit your application. The
SM-1 isolators can also be placed on pedestals to
increase the height of the isolation system.
Pricing & Specifications |
Press
Release: Minus K Receives Laser
Focus World Innovator Award for Ultra-Thin, Low-Height
CT-1 Vibration Isolation Platform

The awards
were given to companies or organizations that demonstrated excellence in a
product or technology, an application, or in research and development.
(November 25, 2019,
Inglewood, California) - For the second year, Laser Focus World held its
Innovators Awards program, which celebrates the disparate and innovative
technologies, products, and systems found in the photonics market. The awards
were given to companies or organizations that demonstrated excellence in a
product or technology, an application, or in research and development.
Full
release...
 |
|
Vibration Criterion (VC)
Curves-Lab Analysis Codes and curve descriptions for different
vibration environments and solutions.
The VC (Vibration Criteria) curves were
developed in the early 1980s by Eric Ungar and Colin Gordon. They were
originally developed as a generic vibration criteria for vibration-sensitive
equipment for use in the semiconductor, medical and biopharmaceutical
industries, but have found application in a wide variety of technological
applications.
The criteria takes the form of a set of one-third octave
band velocity spectra, together with the International Standards Organization
(ISO) guidelines for the effects of vibration on people in buildings. The
criteria apply to vibration as measured in the vertical and two horizontal
directions.
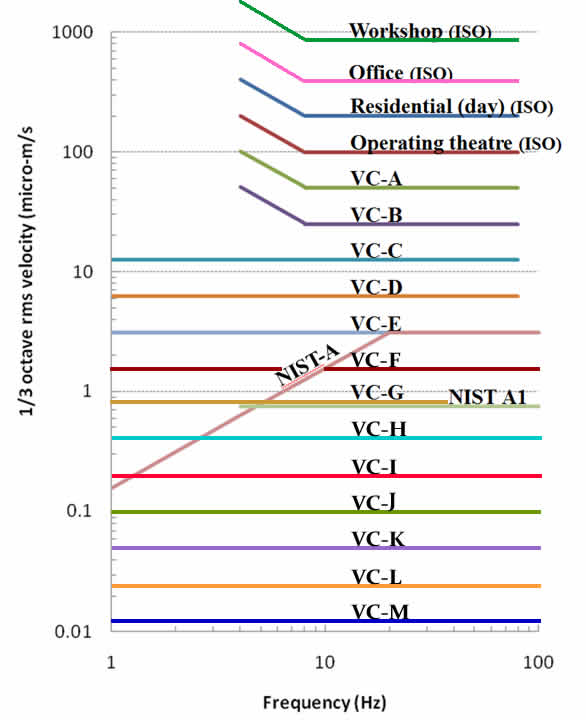
The NIST-A criterion was developed for
metrology, but has gained popularity within the nanotechnology community. The
NIST-A criterion is a very difficult criterion to meet at some sites with
significant low-frequency vibrations.
The VC curves are now widely
accepted throughout the world as a basis for designing a facility to meet the
requirements of a group of highly vibration sensitive equipment used close
together.
University of Michigans Ultra-Low Vibration Lab (ULVL) was
completed in 2014. After the construction, a vibration survey was done on the
Ultra-Low Vibration Lab chambers. The measurements demonstrated that even when
a single vehicle was driving on a nearby street, the vibrations exceeded the
NIST-A specifications necessary for the ULVL.
The University of
Michigan ordered seven customized tabletops and 31 custom Minus K
Negative-Stiffness vibration isolators with pedestals provided for the eight
Ultra-Low Vibration Lab chambers.
Customized Minus K
Technology Negative-Stiffness vibration isolation table installed in one of the
Ultra-Low Vibration Lab chambers
The final vibration survey by Colin Gordon
Associates (CGA), after installation of the customized Minus K
Negative-Stiffness isolators and tables, showed the measured vibration levels
in all ULVL chambers from VC-K to VC-M at frequencies above 2.5 Hz, well below
the NIST-A Vibration Criterion required.
"VC-M is the lowest we have
ever measured, though we werent able to measure below 2.5 Hz because our most
sensitive sensor wont go lower, due to sensor noise floor," said Hal Amick,
Vice President of Colin Gordon Associates.
The updated
VC Curve on Minus K's
website shows these lower curve levels that were measured by CGA
and have already assisted University of Michigans ULVL with two major
scientific milestones.
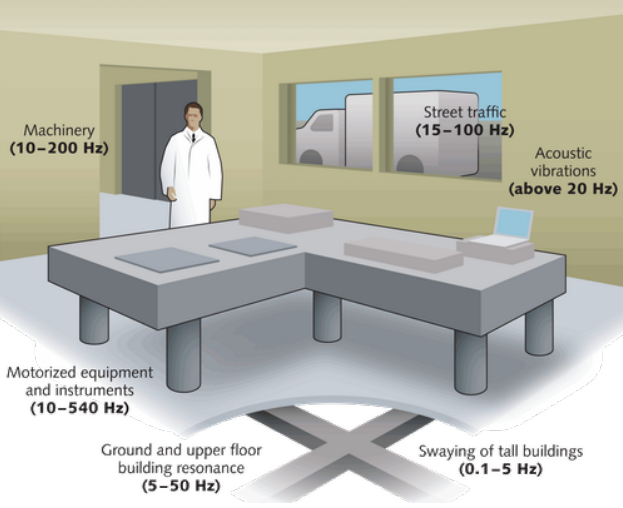 Vibration site surveys can tell you a
lot about how to specify equipment for vibration isolation in your
laboratory.
Updated
VC Curve on Minus K's website... |
How They
Work>>Negative-Stiffness Vibration Isolators
Minus K®
vibration isolators employ a revolutionary concept in
low-frequency vibration isolation. Vertical-motion isolation is provided by a
stiff spring that supports a weight load, combined with a negative-stiffness
mechanism (NSM). The net vertical stiffness is made very low without affecting
the static load-supporting capability of the spring. Beam-columns connected in
series with the vertical-motion isolator provide horizontal-motion isolation.
The horizontal stiffness of the beam-columns is reduced by the "beam-column"
effect. (A beam-column behaves as a spring combined with an NSM.) The result is
a compact
passive isolator capable of very low vertical and
horizontal natural frequencies and very high internal structural
frequencies.
Figure 1 | |
Minus K®
isolators typically use three isolators stacked in series: A
tilt-motion isolator on top of a horizontal-motion isolator on top of a
vertical-motion isolator. A vertical-motion isolator is shown in Figure
1. It uses a conventional spring connected to an NSM consisting of two
flexures connected at their inner ends to the spring and supported at their
outer ends, and loaded in compression by forces P. The spring is compressed by
weight W to the operating position of the isolator, as shown in Figure 1. The
stiffness of the isolator is K=KS-KN where KS is the spring stiffness and KN is
the magnitude of a negative stiffness which is a function of the design of the
flexures and the load P. The isolator stiffness can be made to approach zero
while the spring supports the weight W. |
A horizontal-motion isolation system consisting of two
beam-column isolators is shown in Figure 2. Each isolator behaves like
two fixed-free beam columns loaded axially by a weight load W. Without the
weight load the beam-columns have horizontal stiffness KS. With the weight load
the lateral bending stiffness is reduced by the "beam-column" effect. This
behavior is equivalent to a horizontal spring combined with an NSM so that the
horizontal stiffness is K=KS-KN, and KN is the magnitude of the beam-column
effect. Horizontal stiffness can be made to approach zero by loading the
beam-columns to approach their critical buckling load.
Full article +
more images...
Performance... |
Custom Vibration Isolation
Systems
Minus K engineers can design a variety of custom
vibration isolation systems. Frequently these are modifications of other
designs such as changing the load capacity of an
SM-1 isolator, or the
capacity, size and isolator locations on a
FP-1. Custom table top with four resessed Minus K
CM-1s and
pedestals
Some other custom modifications and
capabilities include:
- Different vertical, horizontal or tilt stiffness in an
isolator
- Different vertical, horizontal or tilt damping in an
isolator
- Vacuum compatibility
- Mildly magnetic
- Heavy load capacities
(Six 10,000 lb isolators for NASA's James Webb
Space Telescope
Ground Testing). - Large displacements
- Large temperature variations
- Compact systems (e.g., a seven-inch cubic 1/2 Hz isolator for a
700 lb payload;
a six-inch diameter by 4-inches tall 1/2 Hz vibration
isolation platform for a 3 lb payload.) - Vertical auto-adjust feature to automatically adjust for change in
payload weight.
- Lock-unlock feature implemented manually with a switch or
automatically
with signals, from a stage motion control system, for
example. | |
Microscopy Vibration
Isolation Tables, Platforms, Benchtops & Custom Systems for
SEM, AFM, TEM, SPM, STM, STEM, NSOM-SNOM
Zeiss Axio
Obersver Z1 AFM on a Minus K
BM-8 | | Delong LVEM5
Desktop SEM on a Minus K
BM-8
|
Nion STEM on a
four-isolator Minus K
FP-1
| | NanoMagnetics
ezAFM on a Minus K
50BM-4
|
|
Many of our clients' microscopes
have nano and micro vibration isolation requirements that are unparalleled in
the metrology world (for
brain
research and at
NASA as examples). Minus K's negative
stiffness and "passive" verses "active" technology, enables microscopes to
achieve their highest level of performance. Our
isolators and
custom systems provide the performance of an
ideal bungee system and the convenience of a bench top system without any of
the problems associated with many of them, including air tables.
From
the ubiquitous bungee suspension systems, to large beds of sand on inner tubes,
there have been many attempts at achieving the ultimate isolation. Air tables
have been used with some success. However, our negative-stiffness isolators
provide superior isolation control and performance while offering better ease
of use and no facility requirements. We even have the flexibility of custom
tailoring resonant frequencies vertically, horizontally and in tilt to your
liking.
Small "active" systems (as opposed to our "passive" systems) are
sometimes used. However, those have several drawbacks:
- They are expensive and fragile.
- They are subject to the noise floor of every component
in the entire feedback loop plus AC line noise.
- They have a limited dynamic range, typically only a few
thousandths of an inch. If this is exceeded (very easy to do) the isolator goes
into positive feedback and you have a very expensive noise generator underneath
your SPM.
- They have to be sitting on an infinitely rigid structure
to work at their theoretical best. Obviously, infinitely rigid structures are
not easy to find in most labs. The result is that the isolator is not always
doing what you think it's doing.
|
Our
isolators give you the best possible
performance in all axes, from high to low frequency isolation. They provide the
performance of an ideal bungee system and the convenience of a bench top system
without any of the problems associated with any of them, including air tables.
We enable our users to achieve the highest level of noise performance possible.
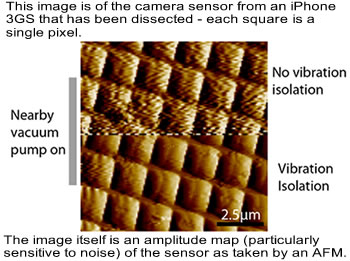
|
|
Previous
Features:
FAQs>>Frequently Asked
Questions About Vibration Isolation
Custom Vibration Isolation
Systems
Audio Reproduction & Turntable
Vibration Isolation
Vibration Isolator Steadies Optics
for NASA Telescopes + Vacuum Isolation
Optical-Laser Vibration Isolation +
video
Optical-Laser Vibration Isolation +
video
Cryostat Vibration
Isolation
Nanoindentation & Micro Hardness
Testing Vibration Isolation
Ultra-Low Frequency Vibration
Isolation Stabilizes Scanning Tunneling Microscopy
Neuronal Research into Animal
Learning, Memory Neuronal Research, Vibration Isolation Problem &
Solution
Sunken Treasure Surrounding The
Coldest Cubic Meter In The Universe Supported by Minus K Vibration
Isolators
Lithium Batteries: Superionic Solid
Electrolytes for Next-Generation
Spacecraft Vibration Isolation On the
Ground
Behavior of a Single Molecule-UCLA's
California NanoSystems Institute
Cleanroom Precision Vibration
Isolation
Negative-stiffness vibration
isolation is utilized to provide ultra-stability for multi-disciplined,
nano-level research at UCLA's California NanoSystems
Institute.
NASA/JWST Update: Custom James Webb
Space Telescope Vibration Isolators Working Well
Audiophile Interests: The Doehmann
Helix 1 Turntable
Minus K Technology Educational
Giveaway to U.S. Colleges and Universities
Articles In The
News
|